Objectives
The overall goal of the TOD project is to demonstrate rapid manufacturability and validation of a full-scale thermoplastic composite door including its surrounding, sub-structure for regional aircraft fuselage barrel. This will be achieved by a tangible step beyond the current state of the art of several thermoplastic manufacturing technologies, some of which are already implemented in other certified aircraft parts. The proposition of TOD project is related to the following:
- Optimisation and validation of component manufacturing using thermoforming and joining processes such as Induction Welding and Resistive Implant Welding, which will enable light weighting by removal of mechanical fasteners
- Take advantage of technology advancement in industry 4.0 automation and on-line monitoring to support higher production rate with high quality performances (Zero defect) and robust control
Development Approach behind TOD project
A process set up stage where the technologies (Thermoforming, Machining, Additive Manufacturing) will be validated at full-scale level will be performed on the final door assembly. The final part of the project will be to carry out a Life Cycle Analysis and Life Cycle Cost Analysis.
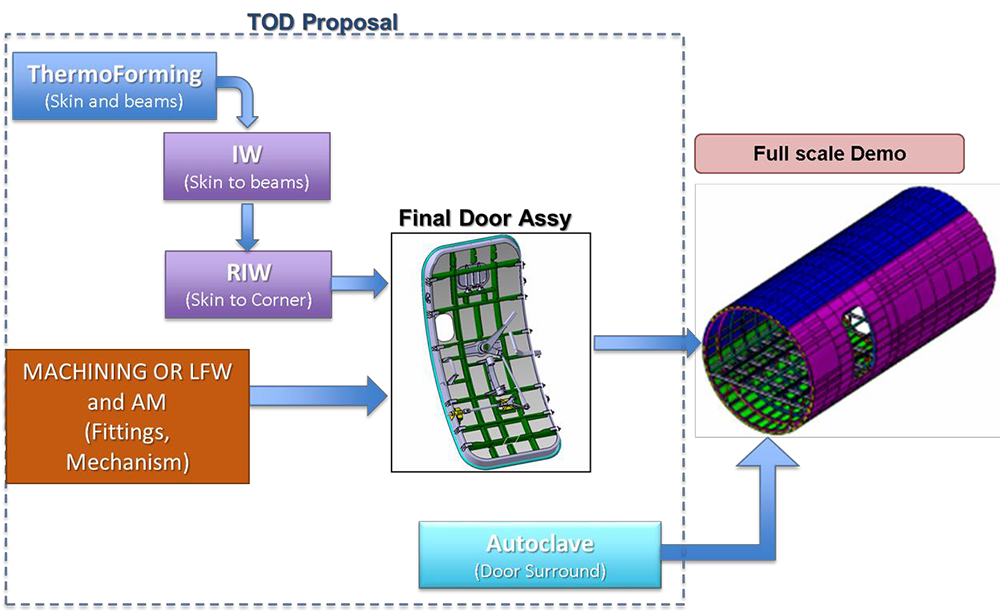
Impact
- The use of thermoplastic materials and the development of out-of-autoclave manufacturing processes are drivers of manufacturing cost reduction and of manufacturing rate increase. These technologies are projected to 75% energy savings over standard autoclave processing
- Minimum 15% weight reduction on structural components as doors. Recent thermoplastic composite studies already demonstrated the substantial weight reduction that can be obtained by combining automated production processes and thermoplastic materials. Specifically, in aircraft related components, an approximate 10% weight reduction of the torsion box of the tail has already been achieved using thermoplastic composites.
- Reduce the Recurrent Cost considering the conception of an adaptive and smart manufacturing equipment to:
- Increased production flexibility
- Decrease the full line tools cost
- Reduction of waste and scrap by 10% by working directly at the defects root cause with a multidisciplinary approach thru the sensors for in-line monitoring directly connected to the manufacturing equipment
- A significant eco-impact reduction through the component’s and aircraft’s life-cycle: the reduction of energy usage during manufacturing of thermoplastics, combined with the light-weighted parts will contribute to the reduction of CO2 emissions during both product manufacture and operation
- TOD address a key issue of extensive use of out-of- autoclave composite with aerospace relevance. The R&D work will generate new scientific knowledge as well as new technologies, and thus strengthen the European positions in this field.
Services
Thermoforming
With respect to the thermoforming process, the parts that are produced are inspected off-line increasing the feedback time drastically. Inline monitoring of pressure, consolidation quality, temperature, etc. can reduce the process development time and increase the process control.
Induction Welding
A fast and flexible joining of 3D structures will be developed to overcome the geometric limits of the standard 1D-2D induction welding process and the onset of defects previously discussed. This will be possible by combining the induction welding system with a jointed-arm robot. In addition, the quality control system will be upgraded through the implementation of a new control system, based on the use of a thermocamera on the welding head, in order to obtain a better control of the surface temperature. Process optimization will be achieved through the development of a multiphysics thermo- mechanical model, in order to obtain the optimal process parameters and to reduce welding defects due to thermal stresses.
Resistive Implant Welding
Addition of the plasma treatment to increase the surface energy of the thermoplastic joining surfaces will be an additional step beyond the state of the art.
Additive Manufacturing of lightweight titanium door locking mechanisms
Combination of Selective Laser Melting (SLM) and Linear Friction Welding (LFW) technologies, which are perfectly compatible, has never been experimented before. The parts of this programme are perceived as ideal for this first realization,
Life Cycle Analysis and Life Cycle Cost Analysis
The comparison of the costs of product caused by the alternatives (materials/processes/etc) will be finalized to identify the cost-effective combination.
An analysis will be conducted to evaluate the sensitivity of the results to changes in the calculation parameters. Specific and definite data for the full scale, i.e. for materials, engineering costs, tooling costs, methods, manufacturing times, equipment workloads and saturation, will be considered
Clustering
SPARE
SPARE-Full scale innovative composite pax and cargo floor grids for regional Aircraft Fuselage barrel on-ground demonstrators
The SPARE project aims to manufacture full scale pax and cargo floor grids for regional Aircraft Fuselage using carbon fibre reinforced composite with thermoplastic matrix. Innovative solutions (Progressive Roll Forming and Induction welding) for highly automated production will be used, thus ensuring weight saving and recurring cost reduction.
This project has received funding from the Clean Sky 2 Joint Undertaking under the European Union’s Horizon 2020 research and innovation programme under grant agreement No 820840. The SPARE project, started in October 2018, is coordinated by OMI S.r.l. in collaboration with CETMA.
https://www.spare-project.eu
COFRARE 2020
Out of autoclave technologies for frame and shear tie of Regional Aircraft (EURECAT-Coordinator, Design Manufacturing SPA, A.ABETE Srl.
WINFRAME 4.0.
Full scale innovative composite windows frames for Regional Aircraft fuselage barrel on-ground demonstrators (EURECAT-Coordinator, SOFITEC AERO SL).